29th Heat Treating Society Conference & Exposition 2017
Department(s):
Materials Science & EngineeringHosted by the ASM Heat Treating Society on October 24 – 26, 2017
Columbus, Ohio, USA
Awards:
Farzaneh Farhadi won Third Place in the Poster Competition.
Presentations
Developing Aluminized coatings on stainless steels by hot dipping
Farzaneh Farhadi, Carl Soderhjelm, Anbo Wang, Prof. Richard D Sisson
Abstract
Aluminide diffusion coatings enhance carburization and oxidation resistance of iron and nickel based alloys by formation of iron and nickel aluminides which extends the life of furnace alloys and fixtures. As a part of a large project in CHTE, an aluminized coating on RA330 was studied by a hot dip process followed by diffusion treatment. Samples of RA330 steel were dipped in pure liquid aluminum at 700 °C for 10 minutes. After dipping, four samples were given an additional diffusion heat treatment. To predict the developed phases, computational analysis was used and the results were compared to the experimental data.
Cyclic oxidation behavior of uncoated and aluminized stainless steels
Anbo Wang, Ms. Jin Guo, Prof. Richard D Sisson
Abstract
High temperature corrosion resistant alloys are widely used for furnace fixtures in heat treatment processes. Aluminizing can be used to increase the high temperature oxidation and carburization resistance of stainless steels. To experimentally investigate the bond strength of the protective oxide to the coating and the coating to the substrate, cyclic oxidation experiments were conducted on the uncoated and aluminized stainless steels. The samples were cycled to 900C in air for one hour and quenched in oil or cooled in air. The weight of samples was measured before each cycle. The oxidation properties and oxide development at high temperatures will be presented. In addition, adherence of alumina scale during cyclic oxidation experiments at elevated temperature will be presented. These samples were characterized using optical and scanning electron microscopy, EBSD, and x-ray diffraction.
A new test method to characterize heat transfer coefficient distribution in industrial gas quenching systems
Yuan Lu, Haixuan Yu, Prof. Richard D Sisson
Abstract
Gas quenching is widely used in aerospace industry when quenching medium or high hardenability steels. High pressure and high velocity gas flow induce complex flow pattern in the furnace. The heat transfer coefficient distribution is localized and affect the cooling rate, microstructure and mechanical properties of the parts. In this paper, a method using bars with proper geometry and steel grades to evaluate heat transfer coefficient distribution in gas quench furnace is proposed. The relationship of the measured hardness at the core of the samples and the outside HTC was investigated by the authors previously. Using this relationship, by simply measuring the core hardness, the HTC distribution in the gas quench furnace can be mapped. It was verified that 0.5” diameter and 4” length AISI 4340 bar can be used to evaluate 2bar nitrogen gas quench furnace. An attempt to measure 20bar helium gas quench furnace was made as well. A basic test procedure was proposed.
Life Extension of High Temperature Structural Alloys RA602CA in Gas Carburizing Atmosphere
Anbo Wang , Haixuan Yu, Prof. Richard D Sisson
Abstract
RA602CA is an oxidation resistant high strength nickel based alloy that has been widely used for furnace fixtures in heat treatment processes. Aluminizing can be used to increase the high temperature oxidation and carburization resistance of nickel-based alloys. In this paper RA602CA and Aluminized RA602CA were selected to study their performance in an industrial carburization furnace for times up to two years. The test samples were exposed in an 0.7wt%C carburizing atmosphere at approximately 900C for 3 months, 6 months, 12months, 18months, 24 months. In this report the microstructural development of both aluminized and unaluminized alloys during the prolonged exposure in the carburizing environment will be presented and discussed. It was found that the weight gain for the aluminized alloys was uniformly less than the as-fabricated alloys.
Identification of the important process parameters to control distortion and residual stress during heat treating
Haixuan Yu, Yuan Lu, Tianyi Zhou, Prof. Richard D Sisson
Abstract
The finite element (FE) model combines a commercially available heat treatment software DANTE to the finite element analysis software ABAQUS have been used to identify the important heat treatment process parameters to control distortion and residual stress. It is found that the Ms temperature of the steel, the temperature dependence heat treatment coefficient of the quenching agent, quenching orientation, immersion speed, quenching temperature, austenitizing temperature and the part geometry are ranked based on their impact. In this paper, the result of these simulations will be presented and discussed. The main purpose of this paper is to provide processing guidelines to control residual stress and distortion
The Tempering Behavior of Carburized Steel
Jin Guo, Tianyi Zhou, Prof. Richard D Sisson
Abstract
The tempering behavior of carburized steels has been experimentally investigated. A variety of steels (AISI 1018, AISI 5120 and AISI 8620) were carburized and quenched to form a 1mm hardened case. These steels were subsequently tempered at temperatures from 200°C to 600°C for times from 15 minutes to 16 hours. The carbon concentration and microhardness profiles were measured for each sample. The results are presented in terms of microhardness versus carbon concentration. The data was analyzed using the Holloman-Jaffe equation as a function of carbon concentration. These results are interpreted in terms of the Holloman-Jaffe constant and microstructural characterization. The results were used to enhance the microhardness prediction in CarbTool©.
The Effects of Heating Rates on the Tempering of 4140 Steel
Xiaoqing Cai, Dr. Lesley D. Frame --Thermatool Corp., Prof. Richard D Sisson
Induction and furnace tempering can be used to achieve equivalent mechanical properties in quenched and tempered martensitic steels. Typically induction tempering takes place at higher temperatures for a short time while furnace tempering is conducted at lower temperatures for longer times. The great difference between these two tempering process is heating rates. This paper presents the experimental results of controlled furnace and induction tempering heat treatments with particular attention to microstructure, mechanical properties for AISI 4140 steel. It was found that the size, morphology, and number density of carbides present determine the mechanical properties and are strongly influenced by the heating rates. These results have widespread impact in several industrial applications relying on both furnace and induction quench and temper processes.
Modeling the Carbon Concentration and Microhardness Profiles in Carburized and Carbonitrided Steel
Lei Zhang , Prof. Richard D Sisson
Abstract
The CHTE surface hardening simulation tools, CarboNitrideTool© and CarbTool© have been enhanced to improve the accuracy of the simulation and to prediction the microstructure and microhardness profile after heat treatment process. CarbTool© can be used for the prediction of both gas and low pressure carburizing process. The prediction has successfully predicted the carbon concentration profiles for gas carburizing process and mostly low pressure carburizing process. In some case, the simulation toll may not work well with the low pressure carburizing process.An improved model for the process is proposed to enhance the boundary condition. In the modeling, carbon potential and mass transfer coefficient are calculated and used.CarbonitrideToolⒸhas been improved to predict the Martensite start temperature (Ms) which can be used for RA prediction. Mixture rule is used then to predict the hardness profiles. Experiments has been conducted to verify the simulation.
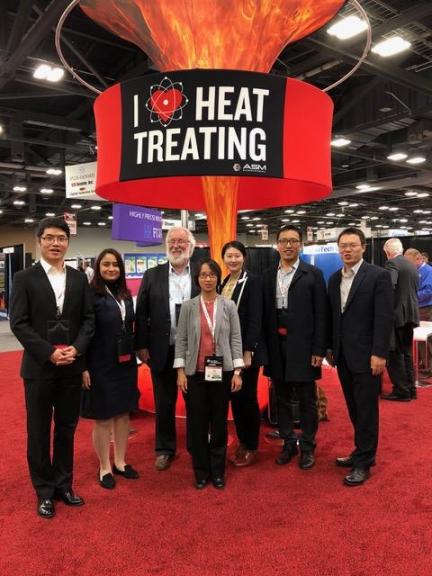