Variable Stiffness Devices and Methods of Use (Hydro Bone)
Description of Market Need:
The Variable Stiffness Devices including Hydro Bone as one possible embodiment can be actively tuned to modulate compressive stiffness. The potential applications of electronically controlled variable stiffness load bearing elements include: (a) active suspensions in automobiles, (b) car seats, (c) advanced structural elements for aerospace industry (wings, blades, etc.), (d) majority of wearable devices such as prosthesis, braces, and exoskeletons, (e) shoe / footwear industry (advanced soles), (f) furniture (beds, chairs, etc.), and (g) various civil engineering structures.
Description of Approach:
The Variable Stiffness Devices are variable rigidity load-bearing structural elements controlled by fluid pressure. This internal fluid pressure applied onto granular media can be finely controlled to adjust inter-particle distances thus in turn finely tuning the compressive stiffness of the entire system. The comprehensive explanation of this phenomenon is provided at
Key Features/Benefits
Benefits:
The Variable Stiffness Devices, including Hydro Bone, are inexpensive, robust, and energy efficient solution for variety of potential applications. They can be easily made in a variety of shapes, weights, and sizes, and they can even have different architectures in order to optimally address required specifications. The granular media can be also simply selected in terms of distribution of particle sizes and their elastic properties to provide desired pressure-stiffness relationship such that device can provide required stiffness range for available range of fluid pressure. Still further, as only very little fluid flow may be needed, small, lightweight, and fast conventional actuators may be sufficient to pressurize the fluid thus making this class of devices a perfect solution for wearable and all other applications where size, mass, and speed matter. Numerous experiments with Hydro Bones showed that stiffness can be effortlessly tuned extremely fast across very large range of stiffness values with very high level of accuracy and in strictly repetitive manner. No substantial effects of wear have been observed so far.
In terms of potential applications and benefits, Hydro Bones can be added to almost any device or surface interfacing with a human body to improve both function and comfort. For example, tiny Hydro Bones can be fitted in shoe soles to intelligently modulate stiffness across foot from step to step. Or same technology can be used for prosthetic socket and braces. Still further, the Hydro Bones can be used as loadbearing structure moving together with a human body, i.e. an exoskeleton worn by soldiers, construction workers, and others who often have to carry heavy equipment. Exoskeleton can make adjustments when less weight is being carried, meaning that it can quickly transition (in less than 100 ms) from a completely flexible structure that allows for greater mobility to a fully rigid one that allows for greater load-bearing capability. Finally, Hydro Bones can be used as active suspension system in automobiles or they can be used in aerospace industry as an active variable stiffness element to exchange passive elements (wings, blades etc.) more prone to wear and damage.
Competing Approaches:
There is no commercially available device that can match all beneficial properties and diverse set of applications of presented class of Variable Stiffness Devices including Hydro Bone.
A notable feature of any fluid based system is that a single prime mover, electrical motor can actuate many sub-units whereas non-fluidic systems require one electrical motor per each sub-unit. In the case of a wearable system, a single prime mover can be positioned more proximally to the center of mass without adding distal masses close to the joints. Hydraulic based transmissions are also more easily implemented than gearing mechanisms for pure mechanical transmissions. Still further as very little flow is required a prime mover here can be small, lightweight, and very fast. Finally, these devices are very robust, i.e. not prone to wear, tear, or damage; they are made of naturally elastic and soft materials and their performance do not involve any friction based process.
The Boston Patent Law Association (BPLA) program “Invented Here!” selected this Hydro Bone invention among top 12 patents from more than 12,000 patents granted in New England in 2018 as part of the BPLA’s initiative to honor the region’s newest and most innovative technologies.
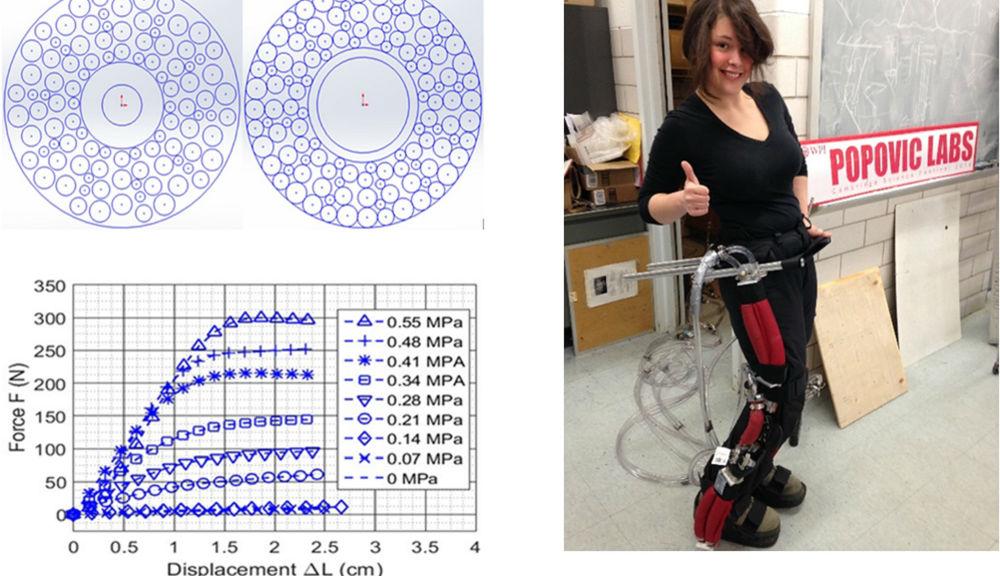
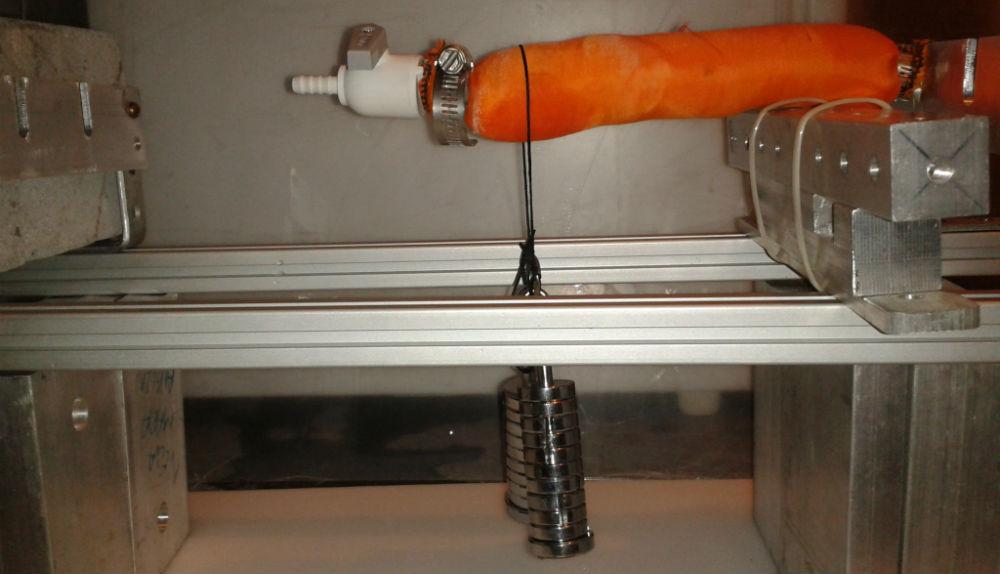