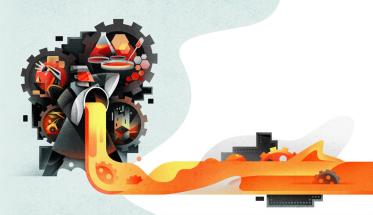
Building Tomorrow’s Economic Renaissance
In 1865, on the eve of the American Industrial Revolution, Worcester was already emerging as a manufacturing hub, with factories turning out everything from textiles to horse-drawn carriages. Recognizing the need for a new kind of professional to lead such enterprises, two local self-made men dreamed of establishing new colleges. John Boynton, a manufacturer of tinware, committed to donating his life’s savings—$100,000—to establish a school that would provide a scientific education to the youth of Worcester County.
Repeated financial setbacks had led one of its city’s most successful industrialists, Ichabod Washburn, owner of the world’s largest wire-making enterprise, to set aside his own plan to establish a school to replace the age-old apprenticeship system for mechanics and other craftsmen. Reluctantly, he cast his lot with Boynton. He pledged to build his rival’s school a working manufacturing facility where students could apply the knowledge they gained in the classroom building, which would be named for Boynton.
Known as Manufacturing USA and formally established in 2014, the initiative represents a $1 billion federal investment
The Worcester County Free Institute of Industrial Science, later renamed Worcester Polytechnic Institute, opened in 1868. Nearly 150 years later, Boynton Hall still stands beside the Washburn Shops, their distinctive towers symbolizing the blending of theory and practice that has always been at the heart of a WPI education.
For nearly a century after WPI’s founding, its graduates regularly ascended to positions of leadership in the nation’s manufacturing enterprises. But as American manufacturing jobs sharply declined, beginning in the 1960s, student interest in the field, along with WPI’s research focus on traditional manufacturing, ebbed. Today, there are signs that the nation may be on the threshold of a new manufacturing renaissance, and the Institute, its professors, and its students appear poised to play key roles. The impetus is a new national initiative to invest in advanced manufacturing industries, accelerate product commercialization, and help prepare a workforce for emerging job opportunities.
Known as Manufacturing USA and formally established in 2014 with support from Congress and President Barack Obama, the initiative represents a $1 billion federal investment to create a network of manufacturing research collaboratives that bring together universities, industry groups, businesses, and government agencies to share research and develop products, technology, and services. To date, 14 public-private institutes have been established, each dedicated to a specific area of advanced manufacturing. Each was launched with $70 million in federal funding, plus matching funds from non-government partners, to kick-start work that will take place over the next five years.
WPI has been named a member of eight of the 14 institutes, making it one of only a handful of universities to play such a prominent role in this high-level initiative. The eight institutes focus on such emerging sectors as lightweight materials manufacturing, regenerative medicine and tissue engineering, robotics, biopharmaceutical manufacturing, clean energy innovation, and integrated photonics.
WPI’s leading role in Manufacturing USA is “a natural connection,” says Bogdan Vernescu, WPI’s vice provost for research, “because these eight fields reflect some of our current research and academic strengths and because our faculty members and students are already engaged in a lot of interesting and forward-looking work in these areas. We were founded by manufacturers for manufacturing-workforce development, so it’s rewarding to think that we are continuing that long tradition.”
WPI has been named a member of eight of the 14 institutes, making it one of only a handful of universities to play such a prominent role in this high-level initiative.
Be Prepared
Manufacturing has evolved considerably since the Industrial Revolution. While many people still picture textile mills, automobile assembly lines, and steel plants when they hear about “manufacturing” jobs, industries and opportunities today span a much wider range of products and services. That’s something even universities—including WPI—have been slow to recognize and support, Vernescu says.
“In meetings with leadership of different Fortune 500 companies, a lot of chief technology officers have told us that we in higher education are not doing enough in preparing a workforce for 21st century manufacturing jobs,”
he notes.
With its new strategic plan, adopted in 2015, WPI has heeded this advice. Taking stock of its research enterprise, the university identified five multidisciplinary research areas for emphasis: health and biotechnology; robotics and cyberphysical systems; sustainable materials and manufacturing; cyber, data, and security science and engineering; and learning sciences and technologies.
Each of these areas encompasses current research strengths, while also embracing emerging disciplines where WPI faculty and students could have a wider impact. As it happens, each also touches on at least one field of advanced manufacturing—an area where novel manufacturing technologies offer the potential for society-changing advances, Vernescu says. In short, the five research themes of the strategic plan seemed tailor-made for Manufacturing USA.
In 2014, as the strategic plan was taking shape, one of the first Manufacturing USA institutes was launched; it also happened to be the first to accept WPI as a member.
Lightweight Innovations for Tomorrow (LIFT) focuses on a goal that is familiar to researchers in WPI’s materials science and engineering programs.
It’s called lightweighting, which Diran Apelian, founder of the university’s Metal Processing Institute (MPI), defines as developing materials from light metals, like titanium, aluminum, and magnesium, or composites like Kevlar, which can perform as well as denser iron, steel, and other ferrous components in cars, trains, planes, spacecraft, and infrastructure.
“By reducing weight, we use less fuel, cut energy consumption, and reduce products’ carbon footprints,” Apelian says. He adds that improved reclamation and recycling of aluminum, another focus of research within MPI, allows manufacturers and suppliers to conserve natural resources and limit new mining, too.
For example, a decade ago a typical car included about 150 lbs. of aluminum. To meet safety specifications, the rest of the frame and body, the engine block, and many other components were made from steel and other heavier metals. Today, through advances in metal casting (including contributions from WPI’s research labs), cars typically contain 350–400 pounds of aluminum alloys, which are one-third the density of steel but just as strong. Ford even makes a pick-up truck with an all-aluminum body.
…for us the payoff is when people are using the technologies we develop here—when someone takes an innovation and applies it and commercializes it.
“We here at WPI have a running record of over 25 years of lightweighting,” Apelian says, referring to the accomplishments of the Advanced Casting Research Center (ACRC), the nation’s first aluminum casting laboratory. Established in 1985 as an industry-university consortium, ACRC today works with 35 industry partners, including aluminum producers and metals casting companies, as well as manufacturers, including Boeing, Harley-Davidson, and Fiat Chrysler, who are increasingly relying on innovative lightweight materials, alloys, or advanced steel to make lighter vehicles.
Once Manufacturing USA opened requests for proposals for its initial institutes, Apelian and WPI collaborated with colleagues at other universities on a submission that emphasized the ACRC’s track record and its industry connections. The pitch, coordinated by partners at The Ohio State University and the University of Michigan, led to the successful proposal for LIFT, which is headquartered in Detroit.
Based on WPI’s expertise with metal processing, Apelian was chosen to lead LIFT’s metal-casting and melt-processing research, one of the institute’s six “technology pillars” (the others include welding and advanced joining and assembly, powder metallurgy, and novel and agile materials manufacturing). Each pillar represents a challenge related to producing advanced lightweight materials on a large scale.
Through LIFT, Apelian and Brajendra Mishra, director of the Metal Processing Institute, currently oversee eight projects at different universities, including several based at WPI. In one, WPI engineers are studying how to directly produce aluminum composite materials from molten metal and chemical precipitates to develop stronger materials that can withstand higher temperatures. That would allow manufacturers to use aluminum alloys in diesel engines without fearing that they might be melted by engine heat. That breakthrough could almost double a diesel engine’s fuel efficiency. In another major effort, WPI and Ohio State researchers are developing and casting ultra-thin-walled, high-strength, die-cast aluminum that can be commercially produced.
So far, LIFT has brought about $2 million to WPI, while helping the university and the ACRC leverage and complement existing funding and support. The expanded portfolio of projects and public and private partners is also attracting more engineers, scientists, and students eager to work at WPI and the casting center.
Ultimately, the success of LIFT and the other Manufacturing USA institutes will be defined by commercialization of technologies and products that serve society and nurture new business, Apelian says. “You can have laboratory innovations and results, you can write papers and publish them, but for us the payoff is when people are using the technologies we develop here—when someone takes an innovation and applies it and commercializes it.”
New Growth
Other Manufacturing USA programs are charting even more novel areas for manufacturing, including regenerative medicine, which holds the promise of healing damaged tissues and organs and producing innovative disease treatments.
Researchers in industry and university labs have been creating engineered versions of skin, muscle, and other kinds of tissue for nearly 20 years, says Kristen Billiar, head of WPI’s Department of Biomedical Engineering. These efforts have led to lab-grown skin grafts to treat ulcers, replacement cartilage cells for use in damaged knees, and an engineered trachea, among other notable successes. But important engineering challenges still need to be solved before the dreams of regenerative medicine can be fully realized.
At WPI, a team led by Glenn Gaudette, professor of biomedical engineering, took a large step toward a solution for one hurdle: the difficulty in getting oxygen and nutrients to cells deep within a growing engineered organ. They discovered a method for removing the living cells from spinach leaves and using the remaining vasculature to support the growth of beating heart muscle.
The breakthrough may ultimately play a role in helping scale up tissue and organ regeneration.
It also highlights one of the ongoing challenges for research teams involved in regenerative medicine: how to take new methods and technologies developed in the lab, often on a small scale, and turn them into manufactured products that can be commercialized.
To address that need, the federal government in December 2016 inaugurated the Advanced Regenerative Manufacturing Institute (ARMI), one of the last of the 14 Manufacturing USA hubs to get under way. With 87 public and private partners, including WPI, ARMI launched BioFabUSA, which is led by Dean Kamen ’73, founder of the New Hampshire-based DEKA Research & Development who is credited with such biomedical innovations as the first wearable medication infusion pump (invented while Kamen was still a student at WPI) and the Luke robotic prosthetic arm.
WPI finds itself once again in the role of helping drive the evolution of manufacturing and manufacturing education.
Still in its formative stage, BioFabUSA has identified five research and workforce training focus areas and is forging relationships between biomedical researchers and biotechnology, so each can better understand the others’ needs. That connection will be a critical link as the institute seeks to support efforts to scale up new and more complex technologies and, ultimately, to build a marketplace and job opportunities. Billiar says he also expects the institute to serve as a forum to standardize and share research and production methods, improve quality control of engineered materials and tissues, and speed up product development.
Billiar and his lab, for example, concentrate on engineering replacement heart valves, a process that began by painstakingly making small samples at the lab bench. By partnering with a company, Billiar now has access to automated fluid-handling robotics that can rapidly and precisely replicate his processes. “And that’s basic compared to what we could do in the future through BioFabUSA,” he says.
The other six Manufacturing USA institutes to which WPI belongs are also in the developmental stage. They include the Advanced Integrated Manufacturing in Photonics (AIM) program, which is dedicated to advancing the technology for manufacturing photonics integrated circuits (PICs) [photonics involves generating and harnessing light and other forms of radiant energy]. Integrated photonics allow designers and manufacturers to put thousands of photonic components (such as lasers, detectors, and waveguides) on a single chip, allowing capabilities that were not previously possible. Under the direction of Douglas Petkie, head of the Physics Department, WPI is building a partnership with Quinsigamond Community College to develop a workforce training, testing, and prototyping center for companies in Central Massachusetts in collaboration with AIM Photonics at SUNY Poly and the AIM Academy at MIT.
Promising Opportunities
As the various hubs of Manufacturing USA launch projects and collaborations, WPI finds itself once again in the role of helping drive the evolution of manufacturing and manufacturing education. And as a member of eight manufacturing institutes, which span a breathtaking sweep of the diverse disciplines that fall under the umbrella of advanced manufacturing, Vernescu says WPI has an opportunity to restore itself and, by extension, its home region to the prominence it once enjoyed in the manufacturing landscape.
“Our vision is to develop a 21st century manufacturing hub here in central Massachusetts,” he says. “While we acknowledge that we are part of eight separate institutes, each with its distinct vision and goals, we also recognize that these eight memberships offer us the chance to create a unique synergy. Already, we are seeing the cross fertilization of ideas across the faculty associated with these eight entities, and we fully expect these connections to lead to new interdisciplinary grant applications, new innovations, and new opportunities.”
Vernescu says the synergy he envisions extends to education and workforce development, which are vital elements of the mission of each of the Manufacturing USA institutes. In addition to creating the new knowledge and innovations that will help build new industries and commercial ventures in the United States, WPI will help prepare students with the skills required for jobs in these novel fields.
“The majority of our undergraduate students are going to work in industry,” Billiar says. “So as these industries grow, they will be well prepared because it won’t just be theoretical stuff, they’ll actually understand the manufacturing processes that these companies are really going to need.”
Looking to the future also means WPI and other partners are already planning for future funding to sustain the initiatives beyond the federal government’s five-year investment. Vernescu says some initiatives will likely prove more successful than others, but successes in commercializing products and applications should help sustain the programs.
Ultimately, the investment, collaboration, and acceleration toward manufacturing industries and innovations represents a “culture change,” Vernescu says. University researchers who think of themselves as scientists and engineers now have opportunities to be manufacturing innovators and leaders and help reinvigorate American manufacturing industries at large.
“Manufacturing has not always been in vogue,” says Apelian, “but, at WPI, we have always taken the view that manufacturing is a critical, transformational, and foundational industry for this nation.” WPI’s wide engagement with Manufacturing USA reaffirms that premise across a new range of disciplines—while connecting the school’s storied past with exciting opportunities for the future. “To some extent we’re building on the legacy of the university,” Apelian adds, “and when you are true to your legacy and what you are good at, it always pays off. And for us, it really has paid off.”
First published in WPI Journal, Fall 2017 edition
This article was originally published in the WPI Journal. For the current issue, please visit the WPI Journal website.